ICD
2017-04-18 10:00
© Burggraf / Reichert
c Burggraf/Reichert

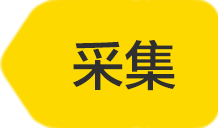
架构师提供的文本描述。斯图加特大学的计算设计和建筑研究所(ICD)和建筑结构与结构设计研究所(ITKE)已经完成了一个新的研究展馆,探索玻璃和碳纤维增强复合材料的建筑规模制造。新工艺基于纤维结构独特的性能和特点。由于这些材料重量轻,抗拉强度高,一种完全不同的制造方法成为可能,它将低有效载荷但远距离的机器,如无人驾驶飞行器(UAV),与强大、精确但有限的工业机器人结合在一起。这种协作概念为大跨度纤维复合材料结构提供了一个可伸缩的制造装置。本研究建立在一系列成功的展馆之上,研究了综合计算设计、工程和制造,并探讨了它们的空间分支和施工可能性。该项目由学生和研究人员在一个由建筑师、工程师和生物学家组成的跨学科团队中设计和制作。
Text description provided by the architects. The Institute for Computational Design and Construction (ICD) and the Institute of Building Structures and Structural Design (ITKE) at the University of Stuttgart have completed a new research pavilion exploring building-scale fabrication of glass and carbon fibre-reinforced composites. The novel process is based on the unique affordances and characteristics of fibre construction. Because these materials are lightweight and have high tensile strength, a radically different approach to fabrication becomes possible, which combines low-payload yet long-range machines, such as unmanned aerial vehicles (UAV), with strong, precise, yet limited reach, industrial robots. This collaborative concept enables a scalable fabrication setup for long span fibre composite construction. The research builds on a series of successful pavilions, which investigate integrative computational design, engineering and fabrication, and explores their spatial ramifications and construction possibilities. The project was designed and fabricated by students and researchers within an interdisciplinary team of architects, engineers and biologists.
© Burggraf / Reichert
c Burggraf/Reichert

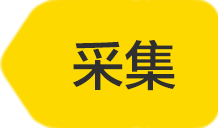
轻质大跨度纤维结构
Lightweight, Long Span Fibrous Construction
纤维复合材料在建筑领域有着巨大的应用潜力。由于性能材料的特点,他们很容易被用于高度工程应用,例如在汽车和航空航天工业。然而,建筑内部的潜力在很大程度上仍未被发掘。在建筑规模生产中,材料自重是对大跨度结构的高度关注,轻质纤维复合材料提供了无与伦比的性能。然而,我们目前缺乏足够的纤维复合材料制造工艺,无法在不影响建筑和设计行业所需的设计自由和系统适应性的情况下生产出如此规模的纤维复合材料。传统的制造方法需要全尺寸的表面模具,并且往往限制了相同零件的系列化生产。此前在ICD和ITKE的研究已经探索了纤维复合材料结构,而不需要表面模具或昂贵的模板。这些新的制造工艺已被用来创造高度分化的多层结构,功能集成的建筑系统和大型元件组件。它们使相对可成形的材料摆脱了传统纤维复合材料制造工艺的限制。然而,这些早期调查的规模受到所使用的工业机器人臂的工作空间的限制。ICD/ITKE研究室2016-17的目标是设想一种可伸缩的制造工艺,并通过为大跨度连续纤维结构开发制造工艺来测试建筑应用的替代方案。
Fibre composite materials have tremendous potential in architectural applications. Due to performative material characteristics, they are readily used in highly engineered applications, such as in the automotive and aerospace industries. The potentials within architecture, however, remain still largely unexplored. Within architectural scale production, where material self-weight is of high concern for larger span structures, lightweight fibre composites provide unparalleled performance. However, we currently lack adequate fibre composite fabrication processes to produce at this scale without compromising the design freedom and system adaptability required for the architecture and design industries. Traditional methods of fabrication require full-scale surface moulds and often restrict the process to serialized production of identical parts. Previous research at the ICD and ITKE has explored fibre composite construction without the need for surface moulds or costly formwork. These novel manufacturing processes have been utilized to create highly differentiated multi-layered structures, functionally integrated building systems and large element assemblies. They have freed the relatively formable material from the limitations of traditional fibre composite fabrication processes. However, the scale of these early investigations has been limited by the working space of the industrial robotic arms that were utilized. The goal of the ICD/ITKE Research Pavilion 2016-17 is to envision a scalable fabrication process and to test alternative scenarios for architectural application by developing a manufacturing process for long span continuous fibre structures.
© Laurian Ghinitoiu
c.Laurian Ghinitoiu

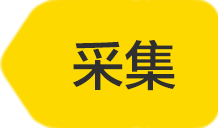
过程仿生研究
Process Biomimetic Investigation
该项目的重点是并行自下而上的设计策略,用于仿生研究大跨度纤维复合材料结构的自然施工过程和开发新型的纤维增强聚合物结构机器人制造方法。目的是开发一种更大跨度的纤维缠绕技术,在充分利用连续纤维的结构性能的同时,将所需模板减少到最低限度。为此,与天津大学进化与生态学研究所和古生物学系合作,对天然轻质结构的功能原理和构造逻辑进行了分析和抽象。两种潜蝇蛾(Lyonetia Clkella)和白翅目(Leucoptera Erythinella)幼虫在弯曲叶片的连接点间旋丝“吊床”,在大跨度纤维状结构的形态和程序原则的传递方面被认为是特别有前途的。从生物角色模型中抽象出几个概念,并将其转化为制造和结构概念,包括:弯曲主动子结构与无芯缠绕纤维增强技术相结合,形成一个完整的复合缠绕框架、大跨度结构上的纤维取向和层次结构以及多阶段体纤维敷设过程,以生成复杂的三维几何形状。
The focus of the project is a parallel bottom-up design strategy for the biomimetic investigation of natural construction processes of long span fibre composite structures and the development of novel robotic fabrication methods for fibre reinforced polymer structures. The aim was to develop a fibre winding technique over a longer span, which reduces the required formwork to a minimum whilst taking advantage of the structural performance of continuous filament. Therefore, functional principles and construction logics of natural lightweight structures were analysed and abstracted in cooperation with the Institute of Evolution and Ecology and the department for Paleobiology of the University of Tübingen. Two species of leaf miner moths, the Lyonetia clerkella and the Leucoptera erythrinella, whose larvae spin silk “hammocks” stretching between connection points on a bent leaf, were identified as particularly promising for the transfer of morphological and procedural principles for long span fibrous construction. Several concepts were abstracted from the biological role models and transferred into fabrication and structural concepts, including: the combination of a bending-active substructure and coreless wound fibre reinforcement to create an integrated composite winding frame, fibre orientation and hierarchy over a long span structure and multi-stage volumetric fibre laying processes for the generation of complex three dimensional geometries.
Courtesy of ICD-ITKE University of Stuttgart
斯图加特大学ICD-ITKE提供

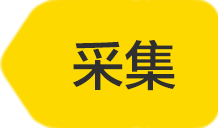
© Laurian Ghinitoiu
c.Laurian Ghinitoiu

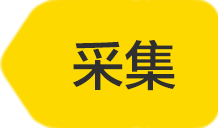
Courtesy of ICD-ITKE University of Stuttgart
斯图加特大学ICD-ITKE提供

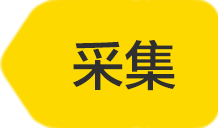
多机网络物理制造
Multi-Machine Cyber-Physical Fabrication
创造一个大跨度结构,超越标准工业制造设备的工作空间,需要一个协作的装置,多个机器人系统可以接口和通信,以创造一个无缝的纤维敷设过程。一根纤维可以在多台机器之间传递,以确保连续的材料结构。制造过程的概念是基于强大而精确的、但范围有限的固定机器与精度有限的移动、远距离机器之间的协作。在具体的实验装置中,两个具有纤维缠绕工作所需强度和精度的固定工业机械臂被放置在结构的末端,而一个自主的、远距离但不太精确的纤维运输系统被用来将纤维从一边传递到另一边,在这种情况下,是一个定制的无人机。将无人机与机器人不受约束的自由和适应性结合起来,开辟了在结构上、周围或通过结构铺设纤维的可能性,创造了仅靠机器人或无人机进行材料安排和结构性能不可行的可能性。
Creating a long span structure, beyond the working space of standard industrial fabrication equipment, required a collaborative setup where multiple robotic systems could interface and communicate to create a seamless fibre laying process. A fibre could be passed between multiple machines to ensure a continuous material structure. The concept of the fabrication process is based on the collaboration between strong and precise, yet stationary machines with limited reach and mobile, long-range machines with limited precision. In the specific experimental set-up, two stationary industrial robotic arms with the strength and precision necessary for fibre winding work are placed at the extremities of the structure, while an autonomous, long range but less precise fibre transportation system is utilized to pass the fibre from one side to the other, in this case a custom-built UAV. Combining the untethered freedom and adaptability of the UAV with the robots, opened up the possibilities for laying fibres on, around or through a structure, creating the potential for material arrangements and structural performance not feasible with the robot or UAV alone.
Courtesy of ICD-ITKE University of Stuttgart
斯图加特大学ICD-ITKE提供

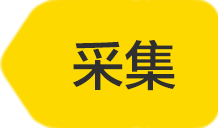

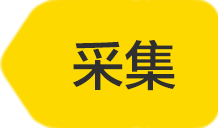
Courtesy of ICD-ITKE University of Stuttgart
斯图加特大学ICD-ITKE提供

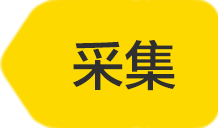
开发了一种自适应控制和通信系统,允许多个工业机器人和无人机在缠绕和纤维铺设过程中相互作用。集成的传感器接口使机器人和无人机能够实时地适应制造过程中不断变化的环境。无人机可以自主飞行和着陆,而不需要人类飞行员,纤维的张力被主动和自适应地控制,以响应无人机和机器人的行为。一个定位系统被用来在机器人和无人机之间创建一个数字和物理的“握手”,以便在整个缠绕过程中来回传递纤维。一系列的自适应行为和集成的传感器为大规模纤维复合材料生产开发新型多机、网络物理制造工艺奠定了基础。
An adaptive control and communication system was developed to allow multiple industrial robots and a UAV to interact throughout the winding and fibre laying processes. An integrated sensor interface enabled the robots and UAV to adapt their behaviours, in real time, to the changing conditions during fabrication. The UAV could fly and land autonomously without the need of human pilots, the tension of the fibre was actively and adaptively controlled in response to both the UAV and robot behaviours. A localization system was utilized to create a digital and physical “handshake” between the robot and the UAV in order to pass the fibre back and forth throughout the winding process. The series of adaptive behaviours and integrated sensors lay the foundation for developing novel multi-machine, cyber-physical fabrication processes for large scale fibre composite production.

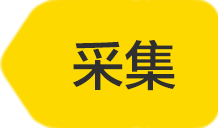
集成演示器
Integrative Demonstrator
ICD/ITKE研究馆2016-17是通过铺设总共184公里的树脂浸渍玻璃和碳纤维而创建的。该轻型材料系统被用来创建和测试一个总长度为12m的单个长跨悬臂梁,作为一种极端的结构方案。地表面积约40平方米,重约1000公斤。实现的结构是在离地制造的,因此尺寸受到限制,以适应一个允许的运输体积。然而,这种装置的变化适用于现场或现场制造,可用于更大跨度和更大的纤维复合材料结构。
The ICD/ITKE Research Pavilion 2016-17 was created by laying a combined total of 184 km of resin-impregnated glass and carbon fibre. The lightweight material system was employed to create and test a single long spanning cantilever with an overall length of 12 m as an extreme structural scenario. The surface covers an area of about 40 m² and weighs roughly 1000 Kg. The realized structure was manufactured offsite and thus the size was constrained to fit within an allowable transport volume. However, variations of the setup were found suitable for on-site or in situ fabrication, which could be utilized for much longer span and larger fibre composite structures.
© Laurian Ghinitoiu
c.Laurian Ghinitoiu

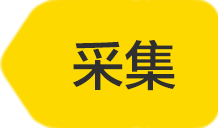
展馆的整体几何结构展示了通过多级体积纤维缠绕制造结构形态的可能性,通过集成弯曲-主动复合框架减少不必要的模板,并通过集成机器人和自主轻型无人机制造工艺来增加可能的建造规模和跨度。它探讨了未来的构建场景将如何演变为包含分布式、协作性和适应性的系统。本研究通过将结构能力、材料行为、制造逻辑、生物原理和建筑设计约束因素结合到计算设计和施工中,展示了计算设计和施工的潜力。原型展馆是一个概念的证明,一个可伸缩的制造工艺的大跨度,纤维复合结构元素,适合于建筑应用。
The pavilion’s overall geometry demonstrates the possibilities for fabricating structural morphologies through multi-stage volumetric fibre winding, reducing unnecessary formwork through an integrated bending-active composite frame, and increasing the possible scale and span of construction through integrating robotic and autonomous lightweight UAV fabrication processes. It explores how future construction scenarios may evolve to included distributed, collaborative and adaptive systems. This research showcases the potential of computational design and construction through the incorporation of structural capacities, material behaviour, fabrication logics, biological principles and architectural design constraints into integrative computational design and construction. The prototypical pavilion is a proof-of-concept for a scalable fabrication processes of long-span, fibre composite structural elements, suitable for architectural applications.

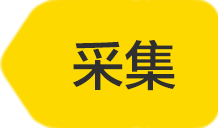

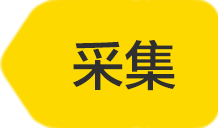

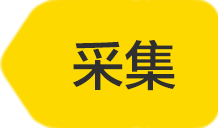

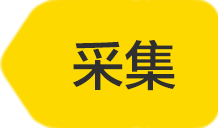

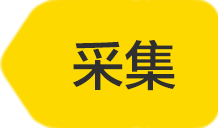

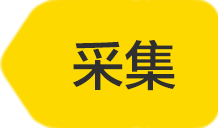

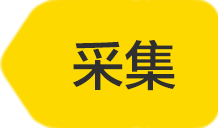

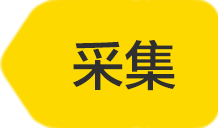

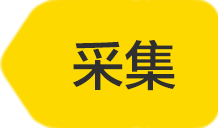

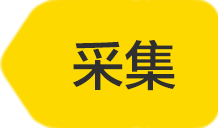

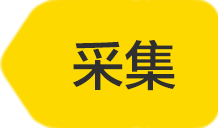

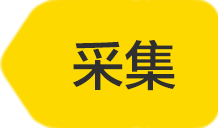

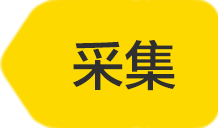

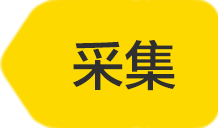

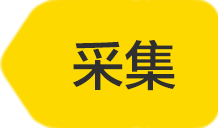

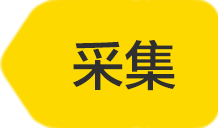

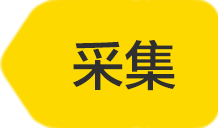

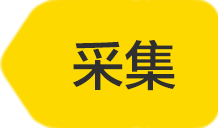

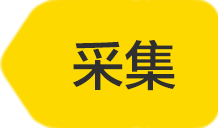

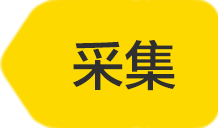

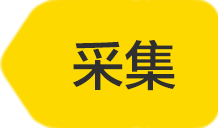

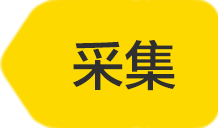

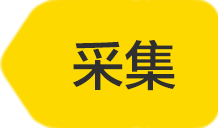

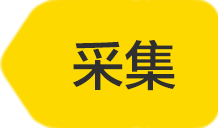

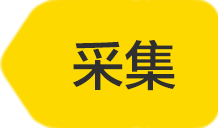

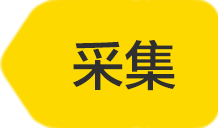

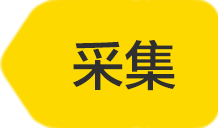

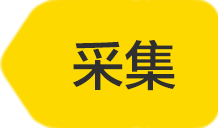

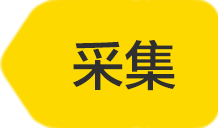

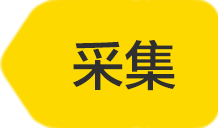

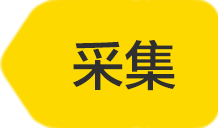

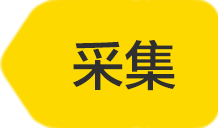

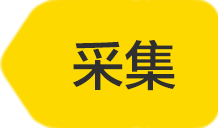

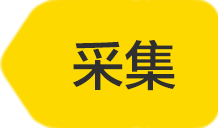

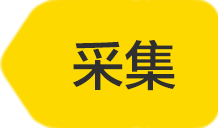

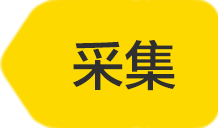

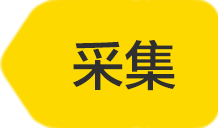

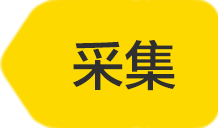
Architects ICD/ITKE University of Stuttgart
Location Stuttgart, Germany
Category Small Scale
Project Team ICD Institute for Computational Design and Construction – Prof. Achim Menges ; ITKE Institute of Building Structures and Structural Design – Prof. Jan Knippers
Area 40.0 m2
Project Year 2017
Photographs Laurian Ghinitoiu , Burggraf / Reichert